In einer vierteiligen Serie berichtet Pistor darüber, was es braucht, damit jede Bestellung komplett, zur richtigen Zeit und am richtigen Ort ankommt. Nach dem Wareneingang und der Kundenbestellung geht es nun ums Bereitstellen der Ware am Tag B im Lieferprozess.
Pistor kommissioniert die Ware
Für ihr Caprese-Sandwich bestellte die Bäckerei Müller gestern drei Schalen vom Artikel 6716, den getrockneten Tomaten. Diese werden heute früh aus ihrem Lagerplatz geholt und in den vorgesehenen Kommissionierbereich gebracht.
Pistor Mitarbeiter Besim Zeqiri kurvt mit seinem Rüstfahrzeug und drei Rollbehältern (RB) durch die Gänge des Hochregallagers. Hier belädt er die RB nach und nach mit jenen Artikeln, die ihm das Display seines Fahrzeuges anzeigt. «Wir beginnen hinten im Gang acht mit den schweren Artikeln und fahren bis nach vorne zu Gang eins, wo wir die eher leichten und heiklen Artikel zuladen», erklärt Besim Zeqiri das System.
Ein Leichtgewicht
Der Artikel 6716 wiegt weniger als fünf Kilo und liegt deshalb nebenan im Klein-Coli-Lager (KCL). Dort kommissioniert José Rodrigues im KCL die kleinen Artikel. Startet er einen Auftrag, leuchtet an dem Regal eine Lampe auf, wo er die benötigten Artikel findet. Blinkt die Lampe, weiss er, dass es sich um den letzten Artikel dieses Auftrags handelt. Er quittiert das Blinken und schliesst den Auftrag ab.
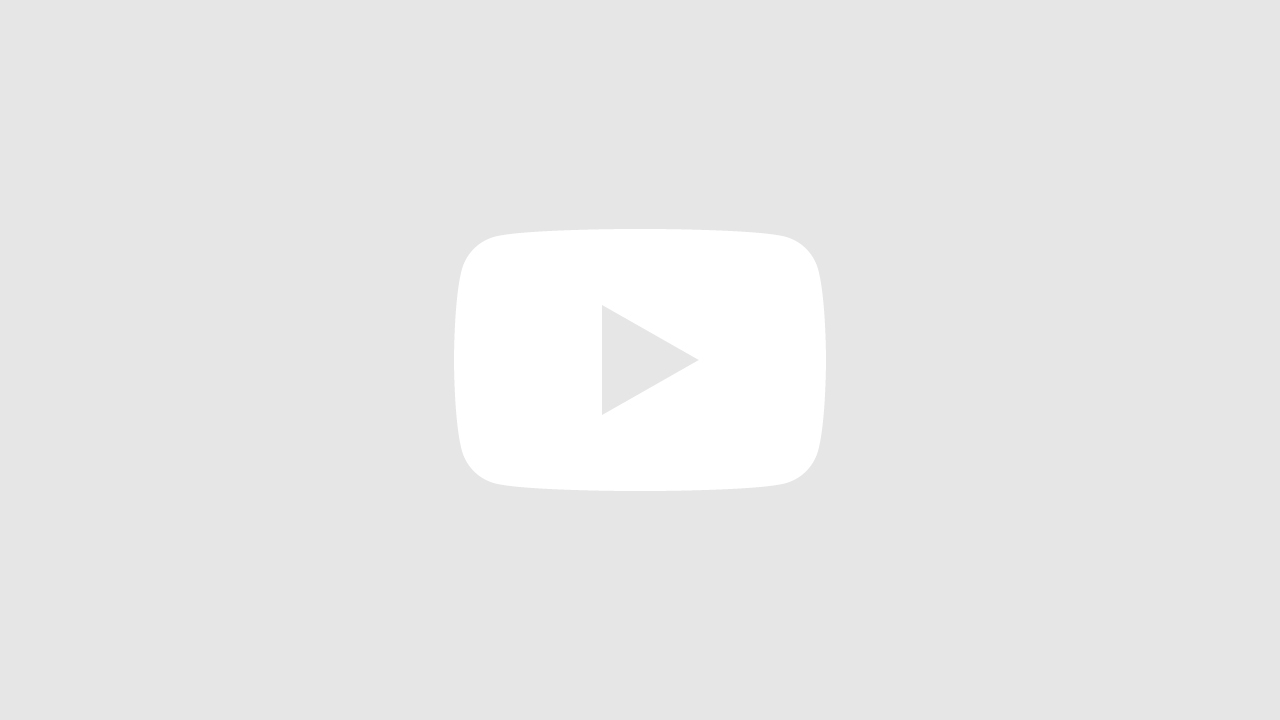
Wir brauchen Ihre Zustimmung
Dieser Inhalt wird von einer dritten Partei gehostet (youtube.com). Um diesen Inhalt anzuzeigen, akzeptieren Sie bitte die Cookies und die Datenschutzerklärung.
Begleiten Sie die getrockneten Tomaten auf ihrer Reise von der Ankunft in Rothenburg durch das hochmoderne Warenumschlagszentrum bis zur Auslieferung.
Gewickelt und gesichert
Hat Besim seine drei RB mit allen Artikeln aus dem Hochregallager beladen, «verdichtet» er sie. Verdichten bedeutet, dass die Ware aus verschiedenen Lagerbereichen auf dem für den Kunden vorgesehenen Rollbehälter zusammengepackt wird. Er scannt die Etikette des RBs, womit er die vorgängig von José kommissionierten Artikel aus dem Klein-Coli-Lager anfordert. Kurz darauf kommt der rote Behälter auf dem Rollband angefahren. Besim packt ihn auf den RB und schiebt diesen in die Wickelmaschine, die die Ware mit einer Folie für den Transport sichert.
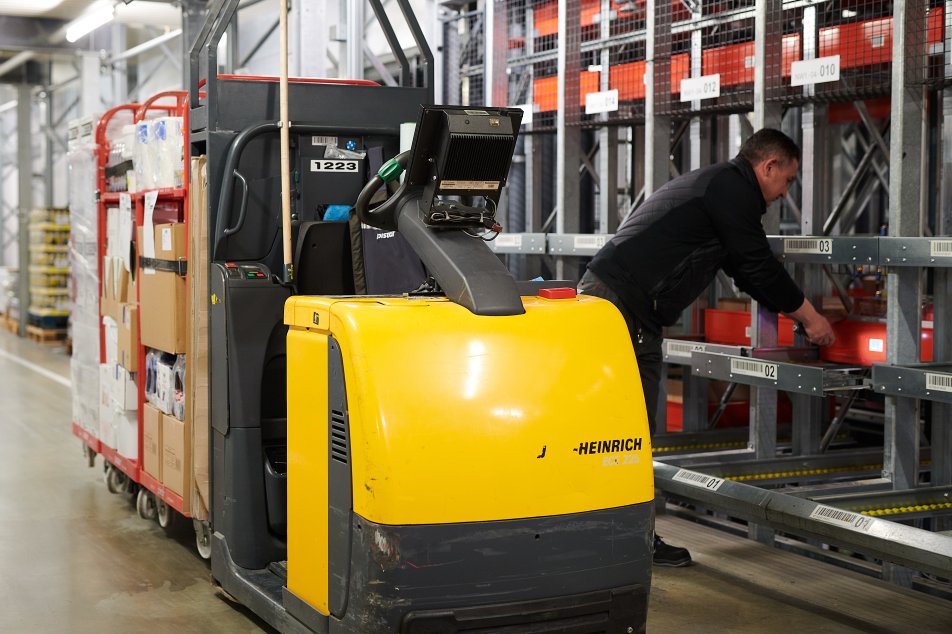
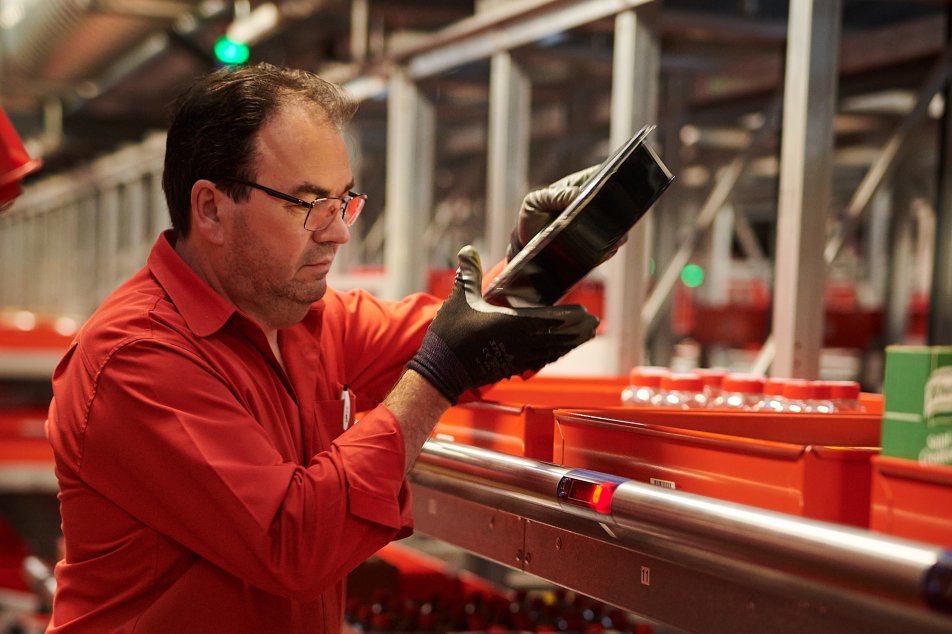
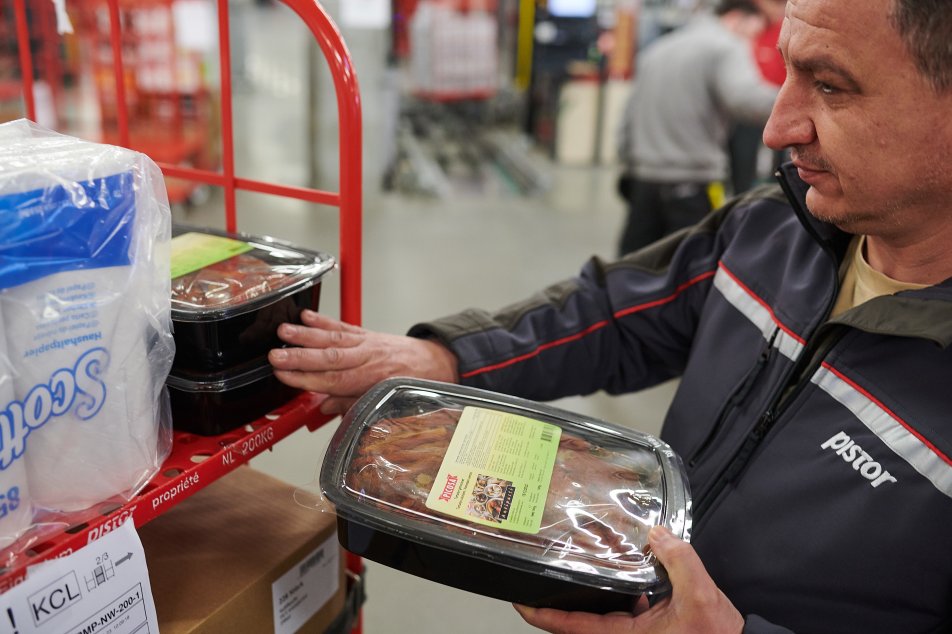
Im Frischelager
Gemäss Matthias Fritschy, Leiter WUZ Mitte, lagern im gekühlten automatischen Kommissionierlager rund 2000 Artikel, darunter Milch, Käse oder abgepacktes Fleisch. An einem der vier Rüstplätze erscheint die Kundenbestellung auf dem Display. Der Mitarbeiter liest ‹drei Pack Emmentaler›, die Kiste mit dem Käse fährt heran, er nimmt drei Pack, quittiert und die Kiste fährt zurück ins Regal. Auf dem Display erscheint die nächste Position: zehn Joghurts. Diese fahren in der nächsten Kiste heran, er packt sie auf den Rollbehälter, quittiert, die leere Kiste fährt weg. Damit ist der erste Teil der Frischwarenbestellung abgeschlossen. Die frischen Tomaten werden erst am Nachmittag angeliefert, umgepackt und ebenfalls hier ins automatische Kommissionierlager geschickt. Dadurch ist es möglich, auch die kurzfristig angelieferte Frischware schnell dem richtigen Empfänger zuzuordnen.
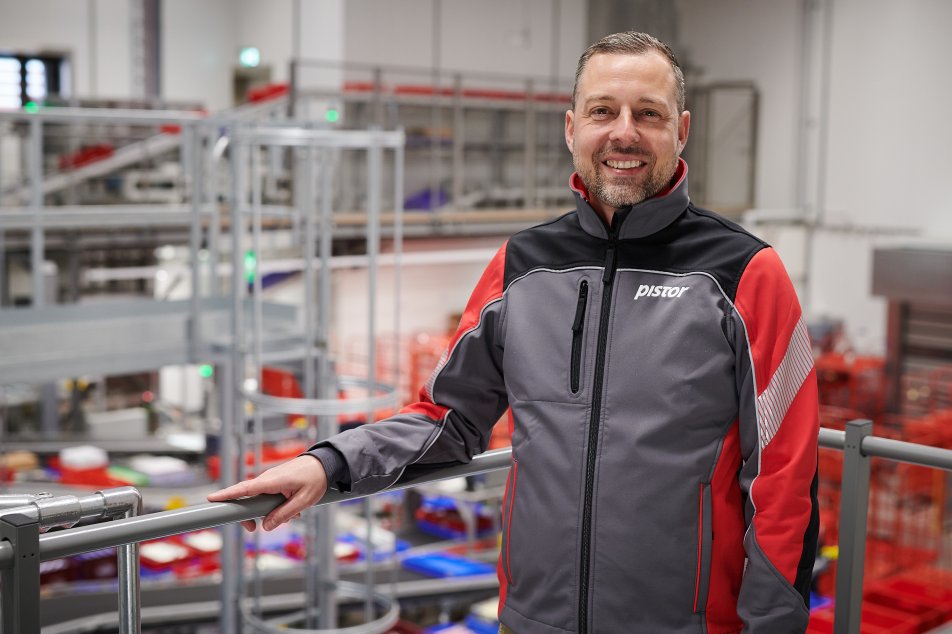
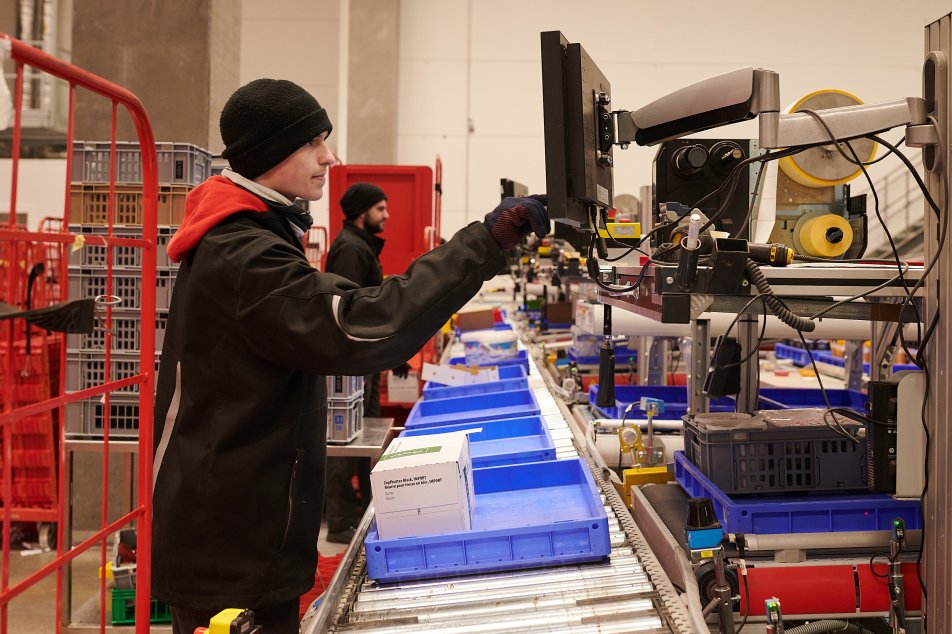
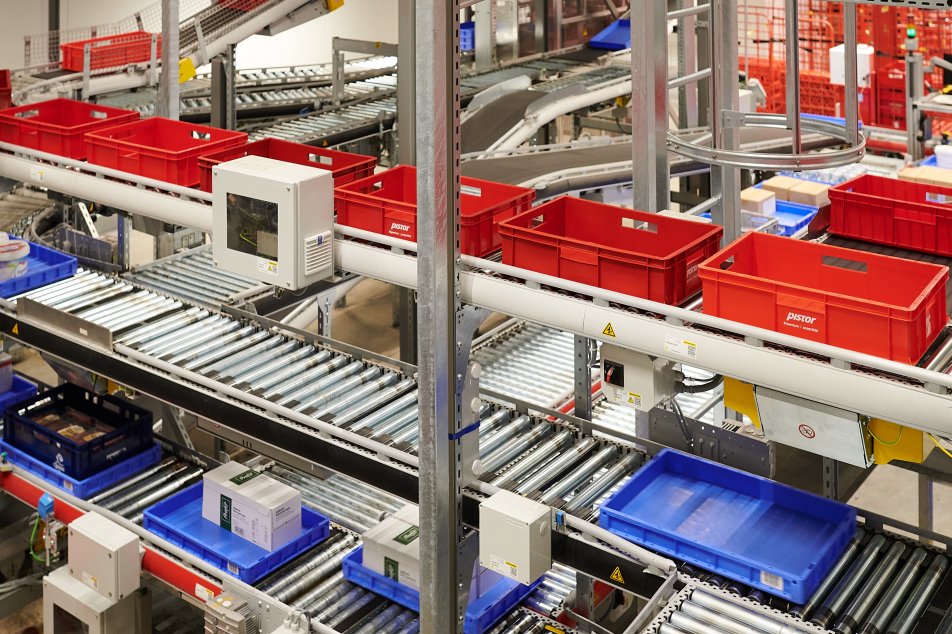
Bei den Tourenplanern
Während im gesamten Warenumschlagzentrum kommissioniert wird, planen die Disponenten die Touren. Das System greift auf Tourenvorlagen zurück und nimmt auf jeder Tour jene Kunden auf, die bis Mitternacht bestellt haben. Es errechnet die Tour anhand Faktoren wie der Distanz zwischen den Abladeorten oder dem vom Kunden gewünschte Abladezeitfenster. Aufgrund von Nachbestellungen müssen jedoch 50 bis 60 Prozent der Abladeorte manuell geplant werden. Denn auch die Dispo-Abläufe sind darauf ausgerichtet, dass die Bestellung am Tag A eintrifft und sie am Tag B auf die Touren von Tag C verplant werden kann.
Bilder: Holger Jacob
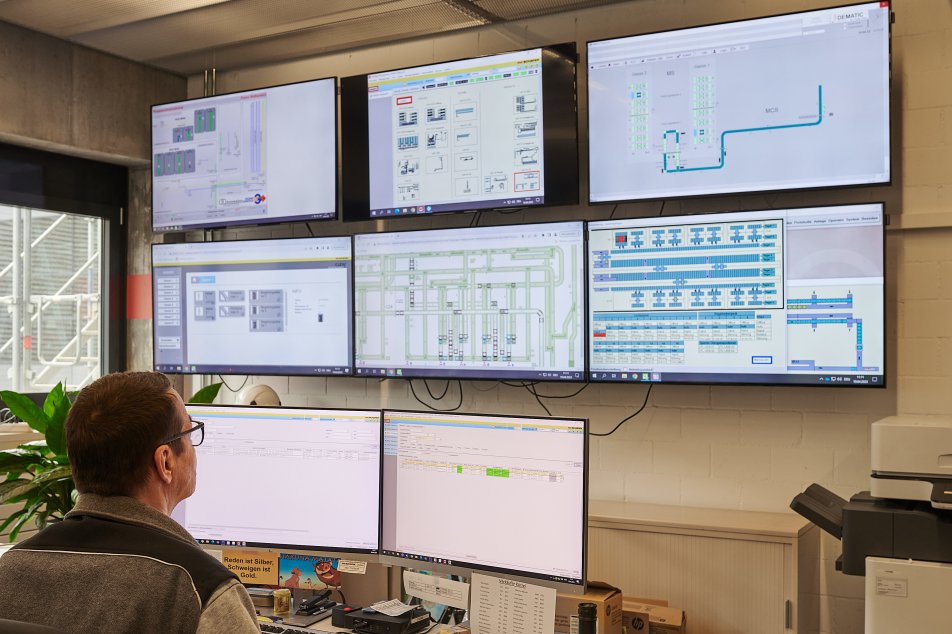
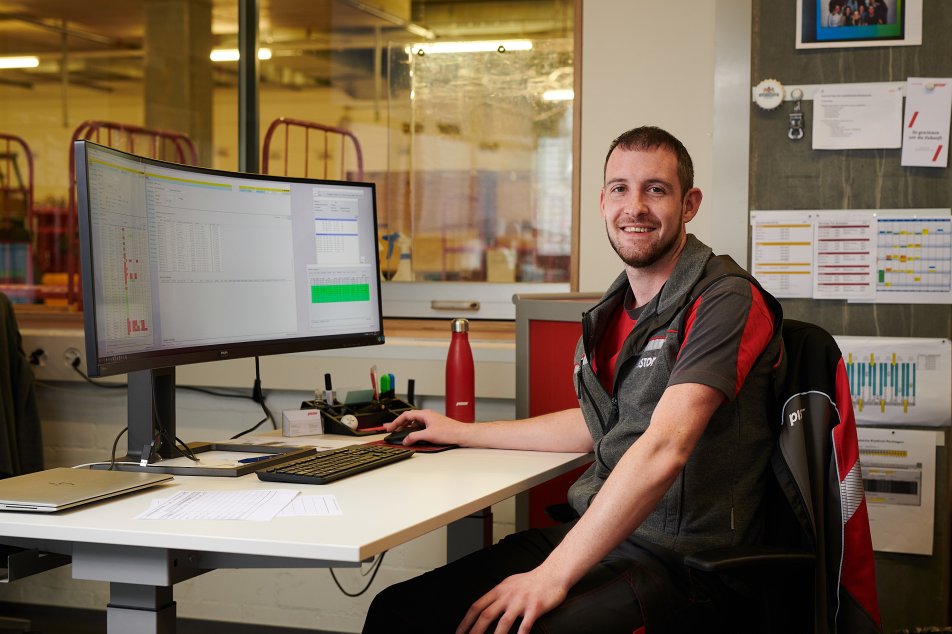
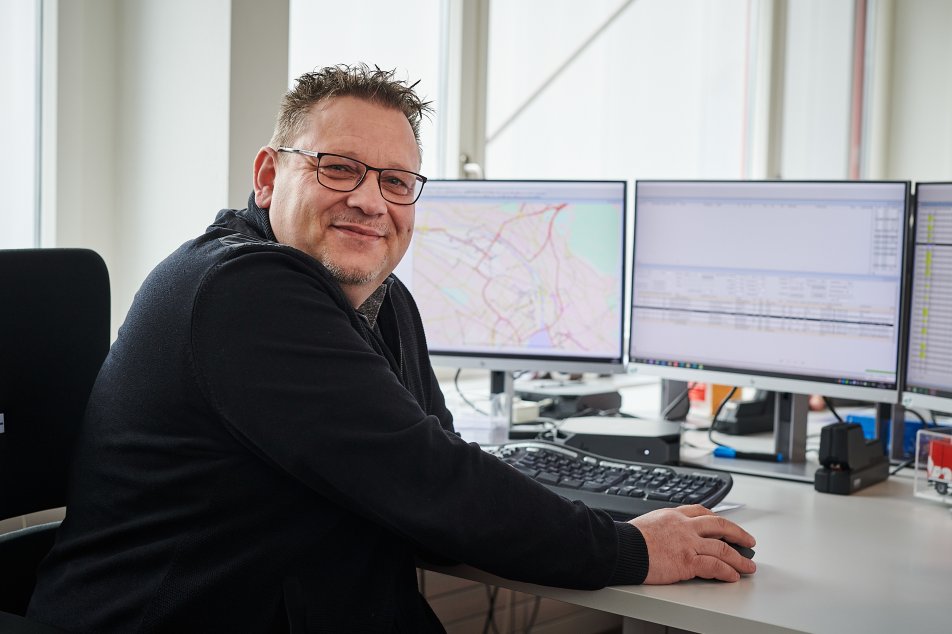